— Paul Iarocci
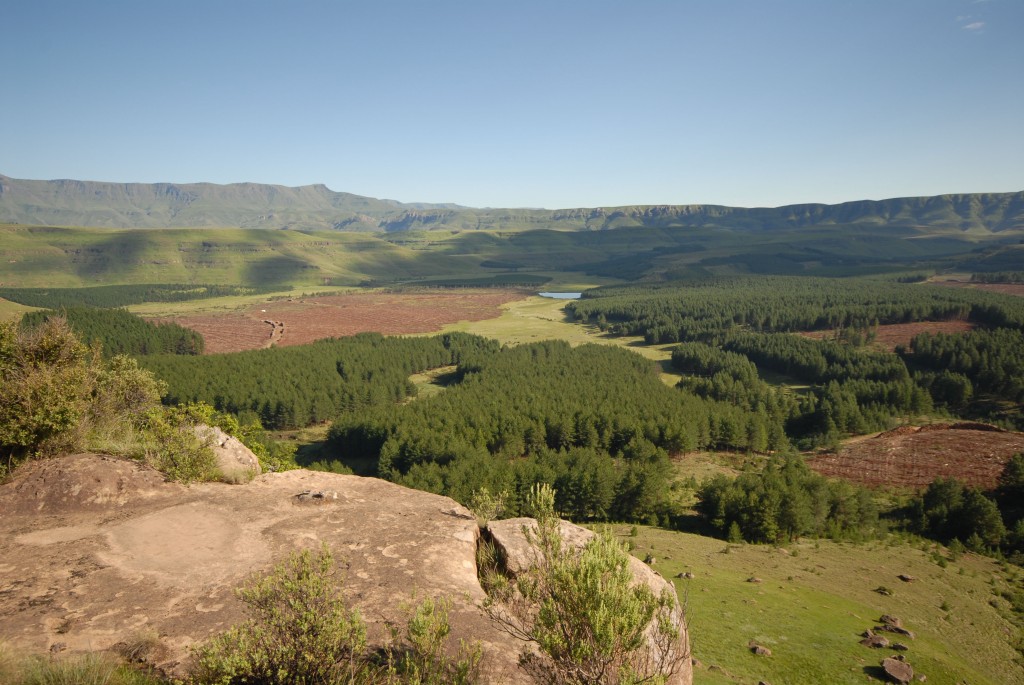
The slopes and valleys that lie adjacent to the Drakensberg mountain range are a patchwork of pine and eucalyptus plantations, grasslands and other native flora.
PG Bison, a large, vertically integrated South African company owned by Steinhoff International, manufactures and markets timber, poles, wood-based panel products, decorative laminates and solid surfacing materials. In 2006, it purchased 82 000 ha of plantation and grazing land from South African forestry company, Mondi. The land, in the vicinity of Ugie and Maclear, in a remote part of Eastern Cape and skirting the famous Drakensberg mountain range, is comprised of a mosaic of pine and eucalypt plantations, intermixed with high quality native grassland, well suited to grazing cattle. PG Bison has 5 000 head of cattle grazing the grasslands. The Nguni breed is renowned for its mottled hides. Diverse native species such as Zebra, buck and wildebeest also frequent the area.
The forestlands, occupying about 33 000 ha of the total land holdings, were planted by Mondi in the early 1990s after the land was acquired in parcels from a number of farmers and individual landowners. Although Mondi maintained the plantations, the company never actually commenced harvesting operations.
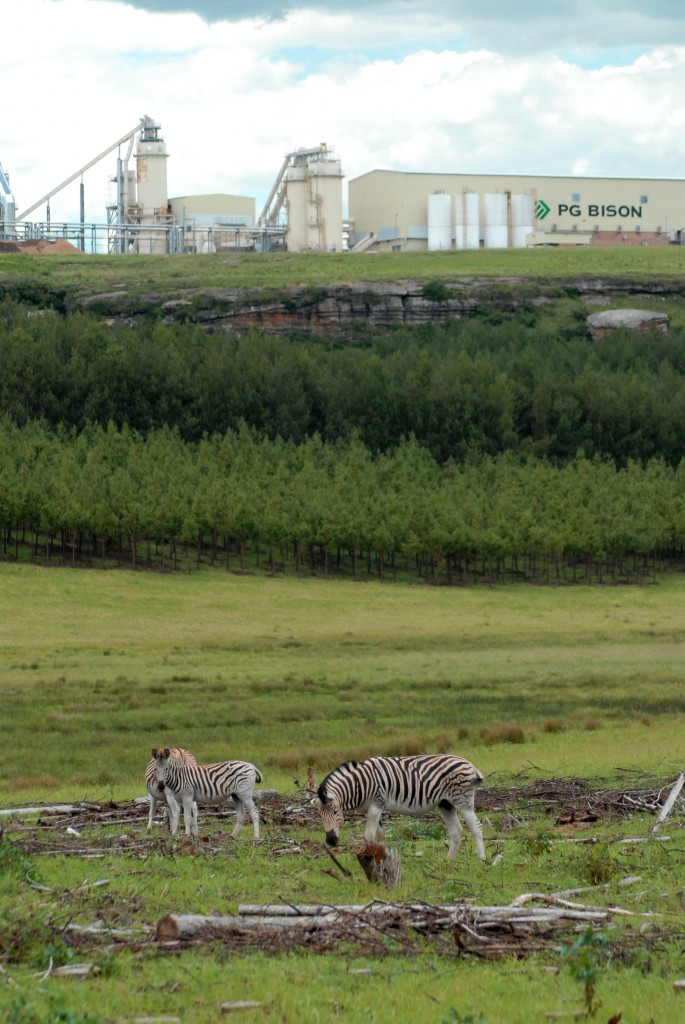
Zebra graze a recently harvested compartment in front of PG Bison’s high tech, continuous press board mill.
By 2008, PG Bison had completed construction of the Ugie Board Plant. The only of its kind in South Africa, the state of the art continuous press board mill utilizes the very latest German technology. Building the mill in a remote, rural community was only one of the challenges that PG Bison faced. On the forestry operations side, the company was basically starting from scratch. As Operations Manager, Pieter de Wet, puts it, “When we started four and a half years ago, this was a green fields operation.”
When PG Bison came to purchase the land from Mondi, the Ugie-Maclear region suffered from extremely high unemployment and poor infrastructure. Additionally, the labour force was unskilled and not ideally suited to operating modern harvesting equipment. “You must remember that we operate in an area with 71% unemployment rate and with very low skills base,” Pieter emphasizes. “So we had to go through a selection process, get the right people and train them even before the machines arrived so as to try and shorten the learning curve.”
Harvesting manager, Mark Wells, weighs in on the challenges PG Bison faced. “When we started here we had no infrastructure at all. We had to build a workshop from scratch. It took a lot of interaction with individuals who had the expertise that were not in the area.”

The LH830C equipped with the Log Max E6. The E6 is proving to be highly effective for debarking 0,15-0,3 m3 stems.
Weighing a myriad of factors, Pieter settled on a CTL harvesting system. One of the primary reasons for a harvester forwarder system was an environmental consideration. The plantations often climb out of wet, environmentally sensitive valleys, necessitating extended transporting distances over soft terrain – not the best options for grapple skidders. “We went through quite a detailed study on the different harvesting systems,” says Pieter. “We operate in one of the most sensitive forestry areas in the country and the cut-to-length is a bit softer on the environment.”
Another factor for Pieter was the structure and geography of the plantations. Falling within a 65 km radius of the mill, the plantation compartments are a patchwork of multiple species of pine and eucalypt stands depending on soil conditions and elevation. In order to harvest in a sustainable way and meet the demands of the board plant and PG Bison’s sawmill customers, the machines are often moving from one small compartment to another and it is necessary to harvest at multiple sites simultaneously. As Pieter points out, “Sure we could have accomplished the same production numbers with a single skidder-feller buncher system, but that would not allow the flexibility that we require.” A single high production system would limit PG Bison’s ability to harvest pine and eucalypt at the same time. In addition, a feller buncher tends to get well ahead of the processors and Pieter explains that having wood sitting for extended periods seriously affects the ability of the processors to debark.
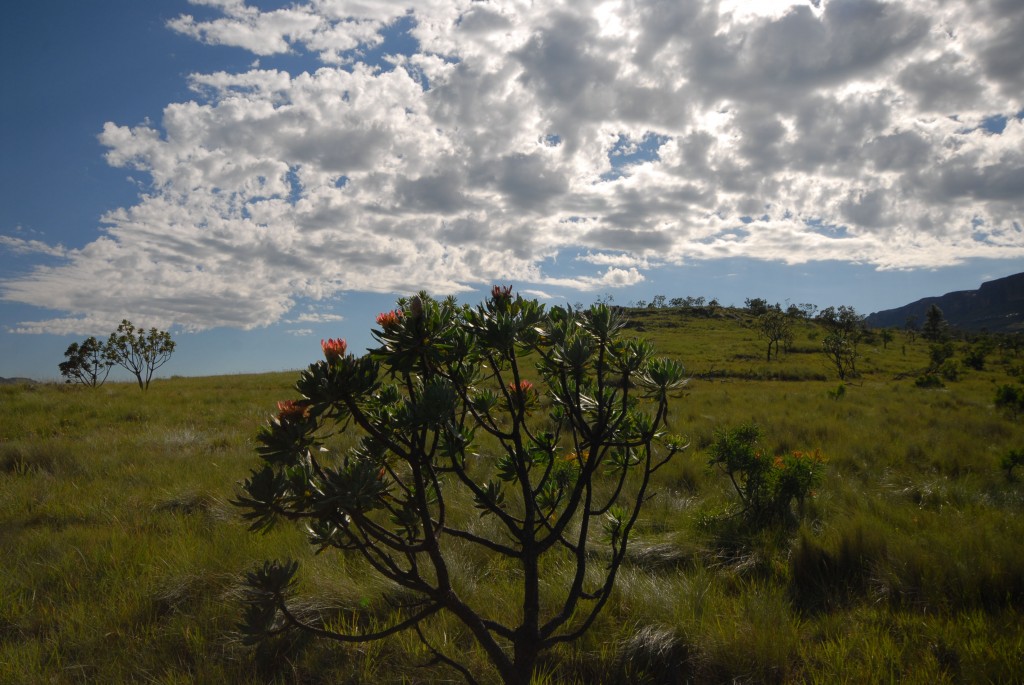
Land stewards. As a major landowner in Ugie, PG Bison not only maintains its plantations and roads but has taken responsibility for large expanses of land that remain in a natural state. The flowering plant, Protea, is native to South Africa.
The board mill consumes 1 500 tonnes of fibre per day and accepts 3 m lengths. To achieve that daily production, PG Bison purchased four CTL systems. The harvesters are either Tigercat H822C or LH830C track carriers with Log Max heads. (The newer E6 is proving to be a particularly capable eucalyptus debarking head for trees in the 0,15-0,3 m3 range.) The forwarders are Tigercat 1065 models. In addition, PG Bison purchased a used LH830C with a Tigercat TH575 harvesting head for felling and processing pine saw logs. Each system is producing on average 20 m3 per hour with stem sizes in the 0,2-0,3 m3 range. In total, PG Bison harvests 450 000 m3 annually. (PG Bison also purchased truck mounted Tigercat 220 loaders for loading trucks.)
Pieter leaned toward the Tigercat brand for a number of reasons but in the end, they mostly relate to uptime. Pieter comments, “We went through quite a rigorous process and the whole issue about training and backup service was a major consideration and why we eventually decided to go with Tigercat machines. I must say that Tigercat came to the party. There were people here when the machines were commissioned and every year so far there were technical courses that we could send our people on.”
Mark adds, “Tigercat was the only company that was actually prepared to give us a commission training period where they would bring in expertise and professionals that were able to help us out and get our operation going.”
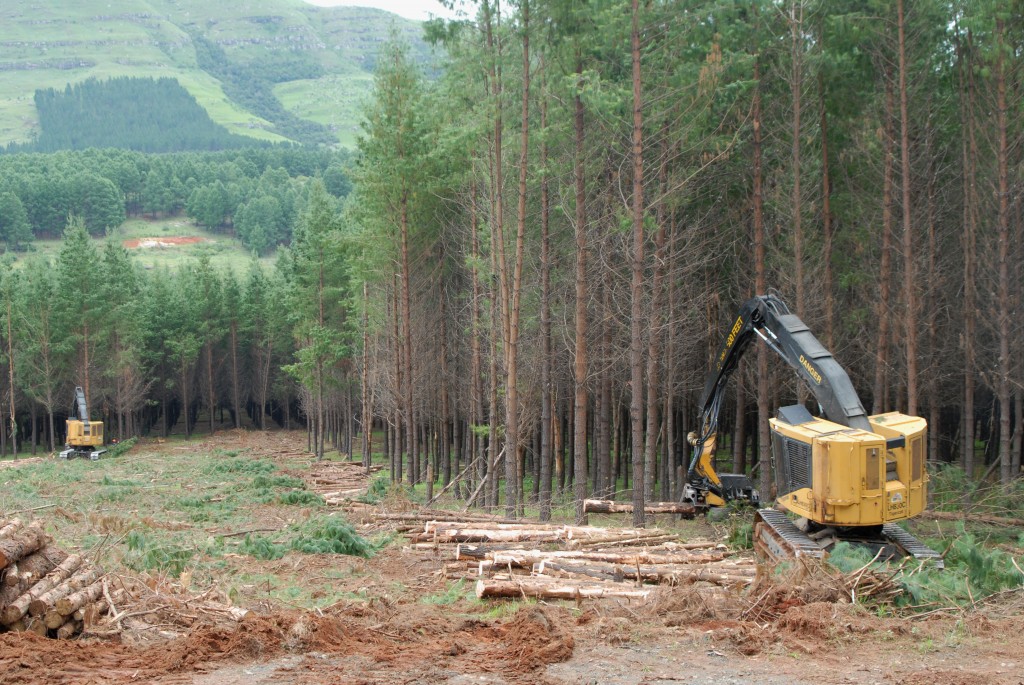
The 822C In addition to the four Log Max equipped harvesters, PG Bison uses one LH830C equipped with a Tigercat TH575 head for harvesting pine saw logs..
Durability was an important requirement because the machines were to be used for operator training. With the high turnover that PG Bison is still experiencing, operator training has been ongoing and continues to this day. One must not underestimate the additional punishment CTL machines suffer when piloted by inexperienced operators. The durability and build quality of the Tigercat product has gone a long way toward maintaining acceptable availability rates as well as overall machine lifespan. “We have been training for four and a half years,” explains Mark. “It has been an ongoing exercise where we’ve introduced new people continuously to the machines. The machines have outperformed any view we might have had from the beginning.”
Pieter especially appreciated that the carriers were purpose-built with proper attention paid to hydraulic efficiencies and cooling capacity. (Summer temperatures can exceed 35°C and, oddly enough, knee deep snowfalls are routinely experienced in winter.)
Another equally important factor is related to the remoteness of the operations. “Due to us being remote, we had a unique risk profile,” explains Pieter. The product support offered by Tigercat dealer, AfrEquip, as well as the direct factory support was far beyond what other suppliers were willing to offer. AfrEquip has a full time service technician, Rudy Ferreira, in place in Ugie to exclusively look after PG Bison’s Tigercat fleet.
People focused
PG Bison is a progressive company and there could be no one better to head operations than Pieter. For a forestry guy, his human resource management skills are exemplary. In May 2011, PG Bison’s Training and Development Centre officially opened. It aims to provide professional and up-to-date forestry training accredited by the Forest Industries Education and Training Authority and the Transport Education and Training Authority.
As Pieter explains, PG Bison’s operator training is open to anyone, not just its own employees. The program takes individuals who may never have driven a car before and teaches them the intricacies of operating harvesters and forwarders as well as teaching basic life skills such as how to manage household finances. PG Bison’s pay scale and benefits are well beyond the average for the community and employee health and safety standards are of paramount importance. The benefits to the community are extensive and difficult to quantify. The company has greatly improved the infrastructure of Ugie and the surrounding area. Overall the PG Bison Ugie operations employ nearly 3,000 local people.
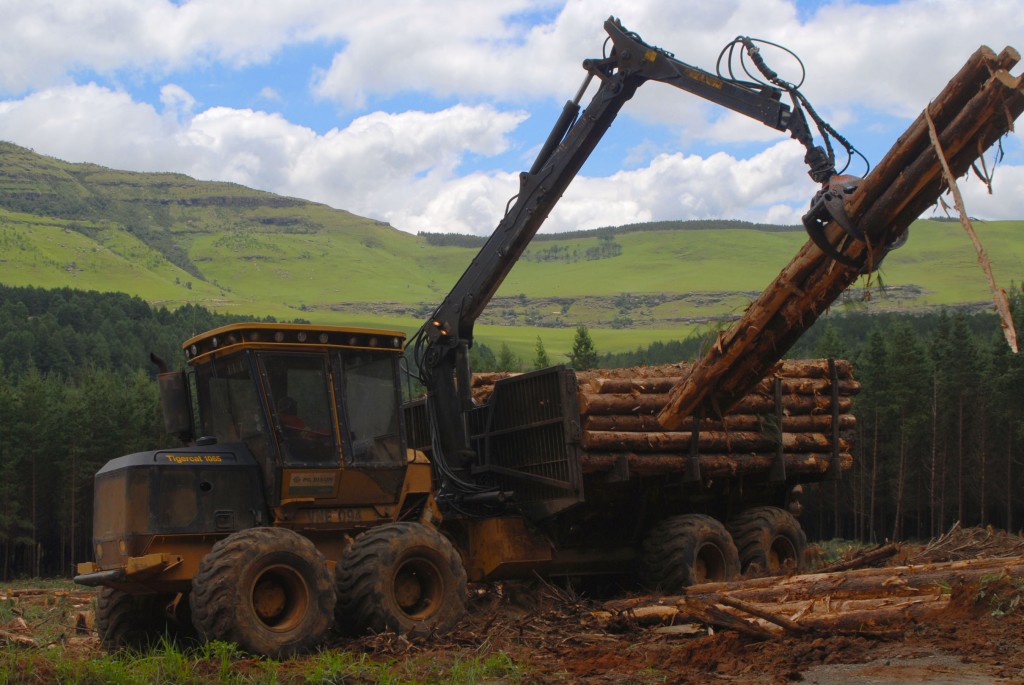
It’s been a tough four years. PG Bison runs four 1065 forwarders. Durability was an important purchase criterion. The machines have had multiple operators and new operator training is ongoing.