– Paul Iarocci
Oscar Uribe and Juan Carlos Torres are the owners of contract harvesting company SOFOSUR LTDA. The Spanish acronym translates as Spanifor Southern Forestry Association. The fifteen-year-old company provides services within the Chilean forestry sector. Based in the important forest industry city of Los Angeles, SOFOSUR’s area of operation covers nearly 700 km (450 mi) north to south from Maule down to Los Rios. Typically, the worksites are concentrated in the Biobío and Araucania regions, usually within a couple hours’ drive from Los Angeles.
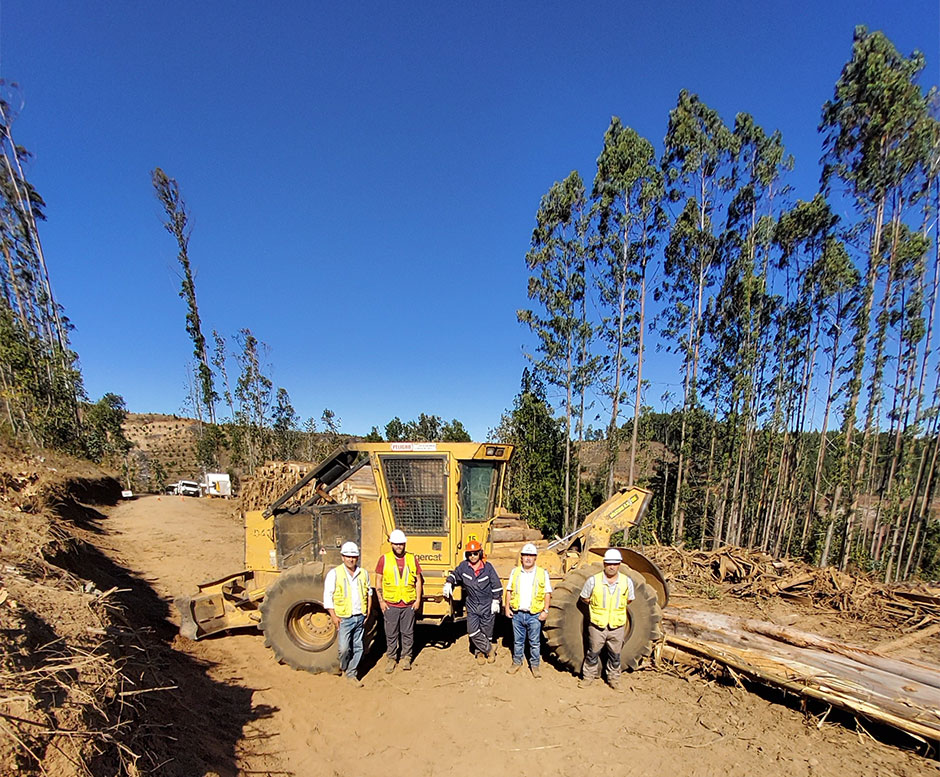
(L-R) Juan Carlos Torres (SOFOSUR co-owner), Alex Vergara (operation supervisor), Segundo Gutierrez (operator), Oscar Uribe (SOFOSUR co-owner), Dagoberto Seguram (driver, personnel transportation).
In addition to forest harvesting, SOFOSUR has recently diversified into an additional business – heavy equipment transportation services for both the forestry and broader general construction sectors. “We recently added two low bed trucks to our equipment fleet for this purpose,” says Oscar.
Chile’s biggest exports are derived from mining, agriculture and commercial fishing, but forest products is probably in the top five. As Oscar says, “Where we are from, it is everything about the forest, so chances that you end up working in a link of the forest industry supply chain are extremely high. We’ve been in the industry since I can remember. I am a former CMPC Companies employee, the company we currently provide services to. And my partner Juan Carlos was always working in the forestry business for different contractors.”
“When we first started in October 2007, we were supporting some small forestry projects here and there for different bigger companies. The first contracts were to build trails in the forests and to prepare for the construction of roads and landing sites,” says Juan Carlos. He explains that at the time, the capital equipment they had acquired for these contracts amounted to a couple of chain saws, an old 604 Deere skidder and a three-wheel logger. It wasn’t until October 2012 that SOFOSUR began to provide direct contract services to CMPC. “Currently, we have contracts for traditional harvesting, mostly on steep or relatively steep slopes ranging from 20-45%.”
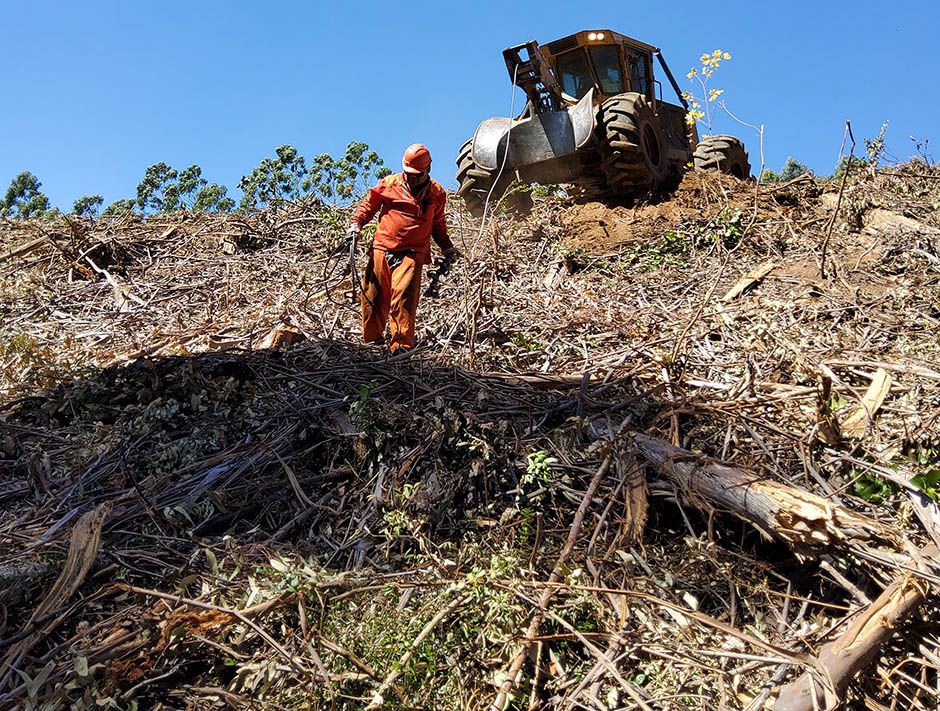
“The places that we work are very steep and difficult to access. Places where sometimes it doesn’t make sense to invest in building skidder trails or to set up a winch as system for a large grapple skidder.”
Traditional harvesting in Chile refers to a motor-manual method. The trees are hand falled and manually delimbed in-stand with chain saws. Cable winch skidders are used to bundle the tree-length logs and transport them to a decking area at roadside. The trees are manually bucked to length and then sorted and piled by three-wheel loggers. At this point, a second contractor takes over the functions of truck loading and transport to the mill. As Oscar says, “It is old school. Chain saws and a couple of guys bundling trees with the winch cable.”
It may be old school, but this niche harvesting function is vital to the bigger picture. As Juan Carlos explains, “The places that we work are very steep and difficult to access. Places where sometimes it doesn’t make sense to invest in building skidder trails or to set up a winch assist system for a large grapple skidder.” Contractors like SOFOSUR help to maximize land utilization and fibre recovery at the best cost.
For Oscar and Juan Carlos, the biggest challenges they face are related to human resources and the high cost of new machinery. When SOFOSUR started contracting to Mininco in 2012, the company employed around ten people. “Today, we have 62 employees, working very closely with indigenous communities,” Juan Carlos states.
CMPC is mindful of both its environmental and social responsibilities, and this mindset extends throughout its supply chain and network of contractors and business partners. The company emphasizes its stakeholder relationships with the indigenous communities local to its forest operations, striving to create shared value. SOFOSUR benefits from CMPC’s close ties to community leaders and the local labour force – the three crews are composed primarily of indigenous Chileans. The cultural and educational programs that CMPC sponsors, as well as infrastructure related programs such as road maintenance, benefit both the relatively isolated local communities as well as contractors such as SOFOSUR by continuing to develop human resources in the forest regions.
Spread among the three crews are eleven machines: four cable skidders including three 604C Tigercat models, one grapple skidder and three Bell three-wheel loggers. Oscar says that in the past, the choice of equipment was very narrow. “Twenty years ago, you had no choice. It was a John Deere machine or nothing. Then big companies started buying Tigercat, and down here, people mimic success.” As the Tigercat machine population in Chile grew, it made it easier and more affordable for smaller contractors to purchase good quality used Tigercat machines.
THEN BIG COMPANIES STARTED
BUYING TIGERCAT, AND DOWN HERE,
PEOPLE MIMIC SUCCESS.
“In 2010, one of our friends got a brand new 604C,” Oscar continues. “We kept an eye on that machine and got direct feedback from the owner. Ironically, we bought that very same machine a couple of months ago.” This, coupled with the fact that Tigercat machines are widely available and well known, made the purchase decision easier for Oscar and Juan Carlos.
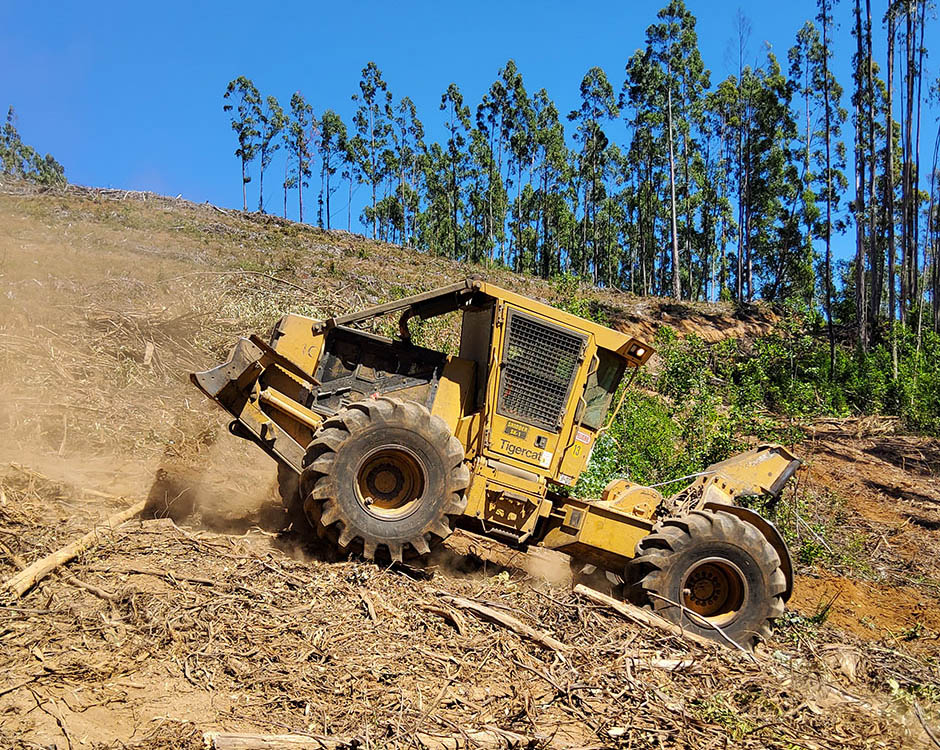
Soil conditions vary widely depending on the season.
“There are more remanufactured components out there, and Tigercat seems to have taken over the business. Plus, I have had the pleasure to meet Ken MacDonald [Tigercat owner and CEO] and also to have key people on the design team like Shawn Pette, Ben Blackman and Mansour Moshiri at my own house,” says Oscar.
In addition, Oscar has another connection to the brand. His son, also named Oscar, has been working for Tigercat for eight years. “I actually visited the factory a couple of years ago when my son invited me to Canada before we owned Tigercat machines. I was amazed by how people are committed to the company. I know firsthand how things are done at Tigercat, and no salesman was required to get me into a Tigercat.”
It is Oscar’s opinion that any machine has the capability to get the job done. What is more important to him is uptime. “If at the end of the day we pulled ten more or ten less cubic metres, it won’t make much difference by the end of the month. But having the machine down for two or three days is very costly.”
So far, regardless of ground conditions, which are extremely wet in winter and very dry and dusty in summer, the Tigercat skidders are meeting all daily and monthly production goals with 90% uptime, factoring in regular maintenance. The machines are all above 10,000 hours, with original axles, drive systems and engines. Daily production averages 600 cubic metres (approximately 600 tn).
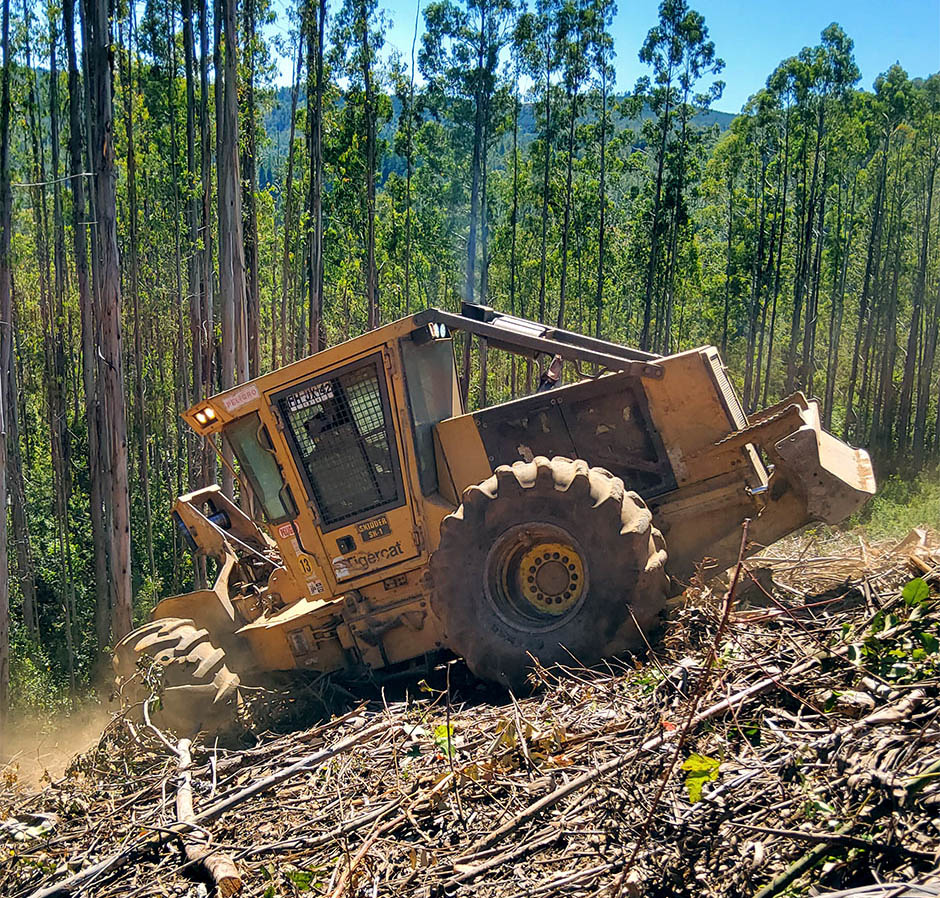
Cable winch skidders are used to bundle the tree-length logs and transport them to a decking area at roadside. The trees are manually bucked to length and then sorted and piled by three-wheel loggers.
Oscar assumed that the operators would have a hard time adjusting to joystick steering, having only operated skidders with steering wheels in the past. “But no, they love the Turnaround seat and having the control in the joystick. It took them a little while to get the feeling for the hydrostatic transmission, but no complaints so far, only good words.”
Next Generation
The junior Oscar Uribe is a mechanical designer in the Tigercat drivetrain group. He is focused on the development of drivetrain components such as gearboxes, differentials, bogies, axles, track drives and pump drives. Oscar has also been involved with the implementation and field testing of hydraulics and control systems within the skidder product group.
Soon after Oscar graduated in Chile with a degree in mechanical engineering in 2013, he applied for a one-year Canadian work permit, intending to explore opportunities to work on new technology development. “I knew about Tigercat through my Dad’s work, and I wanted to improve my English, so Canada seemed to be the perfect place to accomplish both goals.”
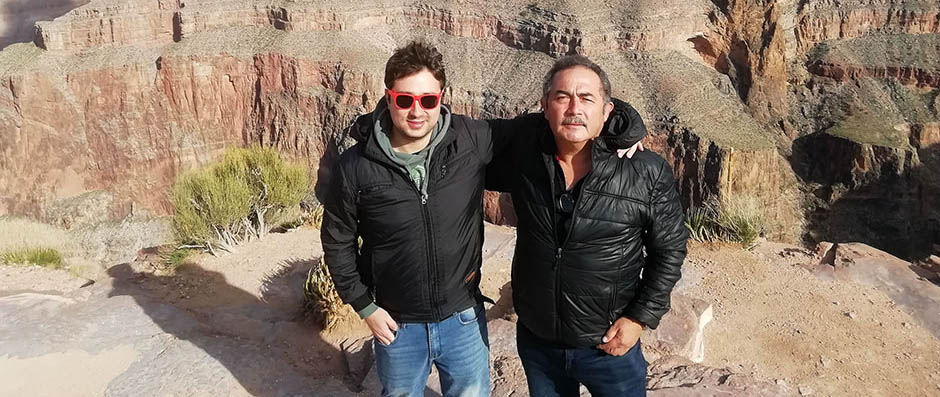
Oscar Junior and Senior.
Oscar’s first stop in Canada was Brantford. He managed to get an interview at Tigercat, but it didn’t go so well. “It was difficult to fully express myself in a language that I was just starting to learn, but I ended up getting a general labour job at the track machine plant in Paris, cleaning up the yard.” Oscar progressed to picking parts for the assemblers and, after six months, was transferred to the drivetrain facility – as his command of English quickly and steadily improved.
“I suppose it was just good timing because there were a lot of projects in the pipeline, drawings to be updated, and so on for this new department.” Coincidently, around the same time, the skidder group was working through some issues in Chile and language barriers were causing a problem for the travelling engineers and technicians. “Someone must have thought it was a good idea to bring me down there so I could get some field experience and help with translating.” Through these trips, Oscar learned about machine programming, hydraulics and electronics. He continued in the drivetrain product group, eventually obtaining immigration documents required to continue working and living in Canada long term as a valued member of the engineering team.